Rock 11
Small in size only
The whole Rock series is designed and built with a structure capable of supporting intensive production loads even over 3 shifts and operating for many years while maintaining high reliability and low maintenance costs.
Rock 11 is proposed for those who work with high production rates. Thanks to the 11th spindle with the possibility of optional liquid cerium, it allows high productivity while maintaining an excellent level of quality.
The high-precision mechanics and the extensive use of cast iron, which guarantees the absence of vibrations, lead the Rock series to higher processing speeds than those of other machines on the market with the same number of spindles.
Rock 11 can perform, with specific tools, also the bevel up to 45 ° with a width up to 10mm.
Advantages
![]() LONG LIFE |
![]() SILENT AND WITHOUT VIBRATIONS |
![]() LOW MAINTENANCE COSTS |
![]() EASY TO USE |
![]() SPEED AND QUALITY OF PROCESSING |
Technical features
Model | Dim. mm | N° wheels | Weight kg | KW | H min mm | Thicknessmm | Speed m/min | Max Weight kg/m | Chamfer mm |
Rock 11 | 8089 x 2340 x 1450 | 11 | 3500 | 25 | 50 | 3-40 | 0,5-5 | 250 | 10 |
Type of wheels

Legenda
![]() Diamantata |
![]() Lucidante |
![]() Gomma cerio/feltro |
![]() Motore con doppia velocità |
AWA features
AWA (Authomatic Wheel Adjustment) is Neptun’s patented system for the fully automatic management of both diamond and polishing wheels.
Thanks to its hydraulic regulation principle, it combines simplicity, precision and consequent reliability over time. Traditional solutions use electric motors in areas subject to water and humidity, which in the long run can compromise their operation.
The AWA spindle adjustment and measurement systems are water resistant in IP67 class.
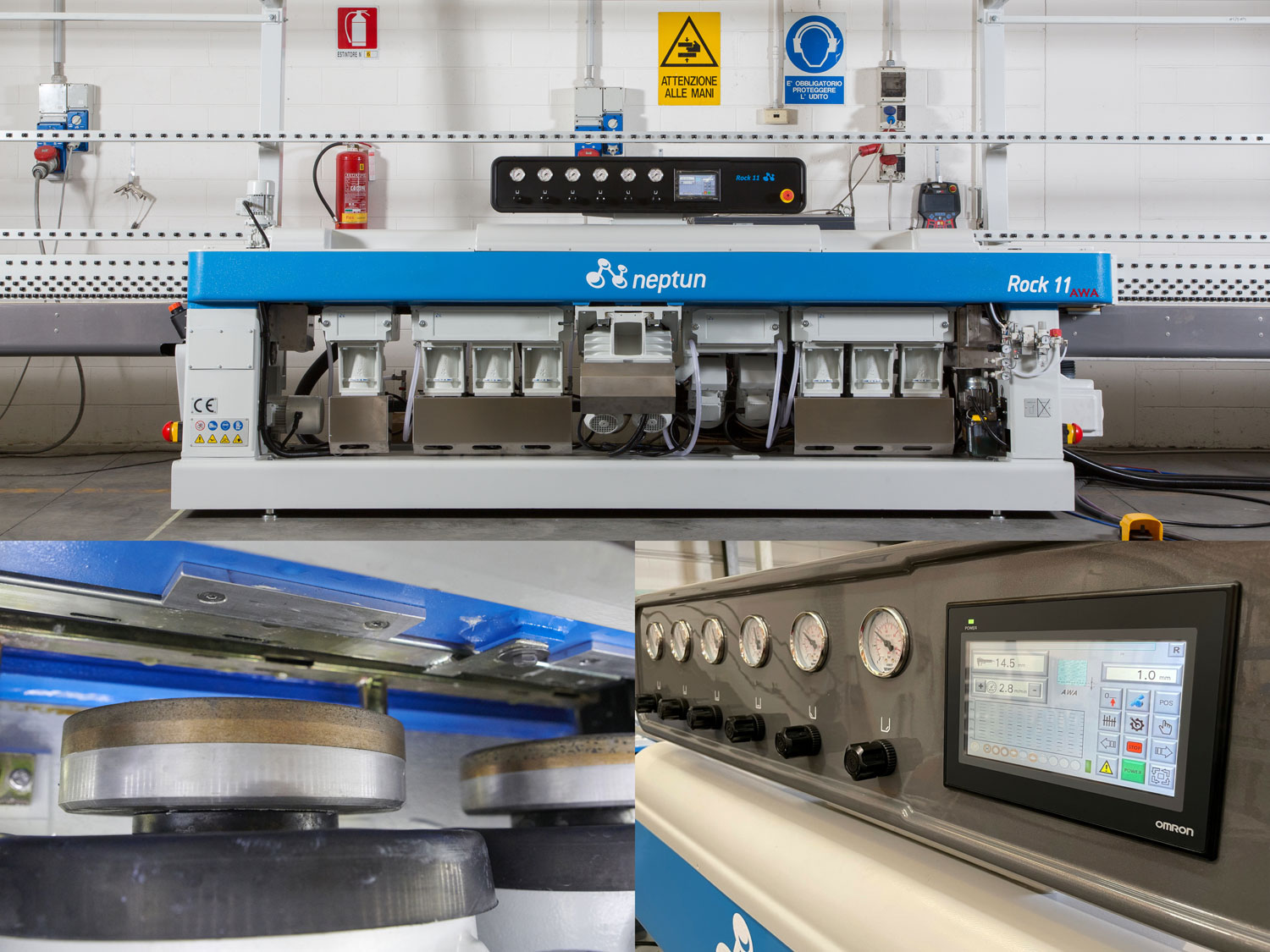
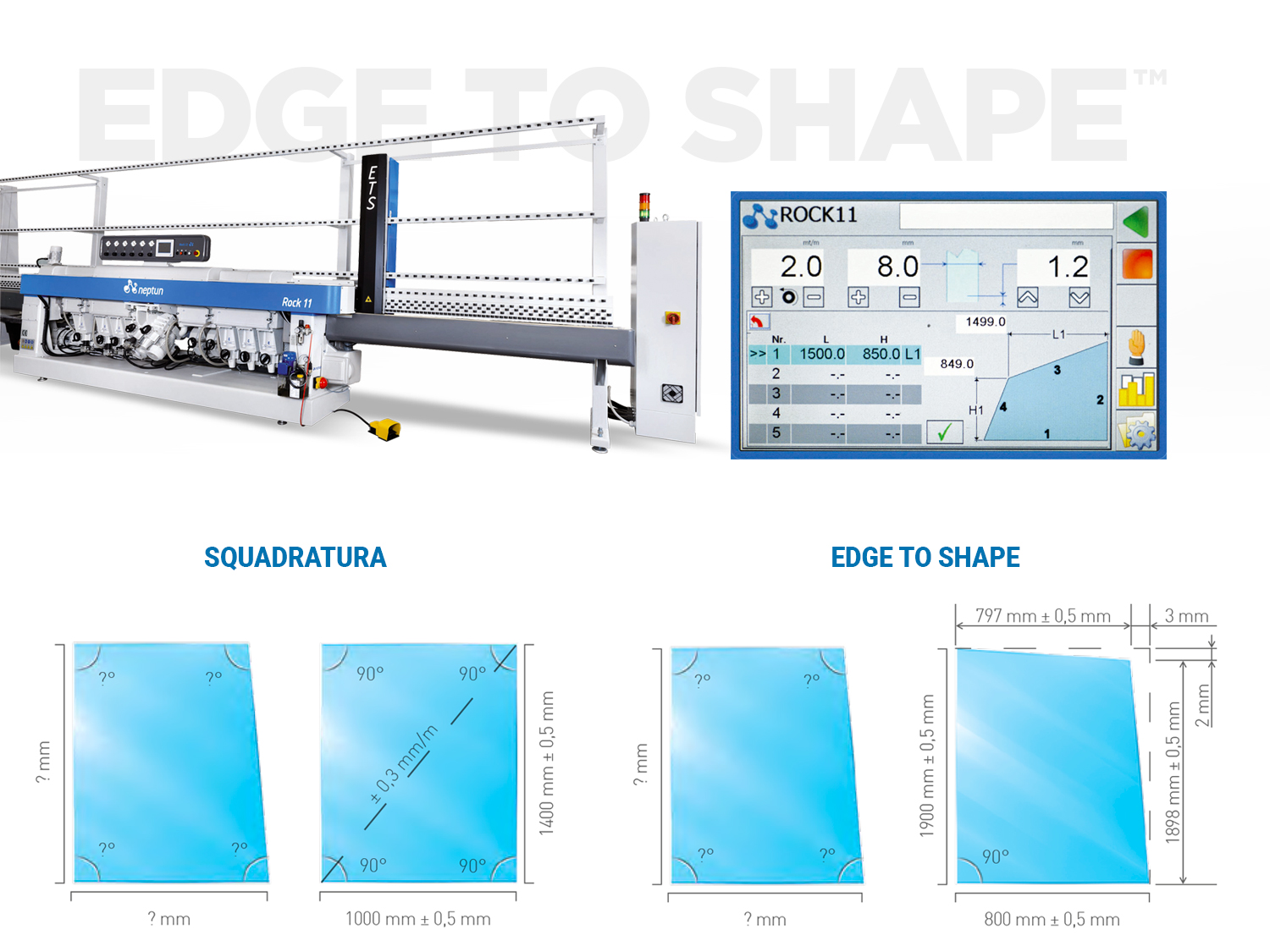
ETS features
Edge To Shape™ is the innovative evolution, conceived by Stefano Bavelloni and patented by Neptun, which allows the straight-line edgers of the Rock series to perform edge processing, with control of the final geometry both in terms of angles and final desired dimensions, also out-of-square.
The sophisticated process consists of scanning the incoming angles by a laser system and adjusting the removal angle by means of specific axes controlled by the powerful CNC. At the same time, the same laser system measures every glass side in real time and the removal angle is consequently adjusted in order to get the desired final dimensions.
According to the production requirements, the operator can choose whether to use the ETS mode or the normal processing cycle.
STANDARD features
Video
Optional
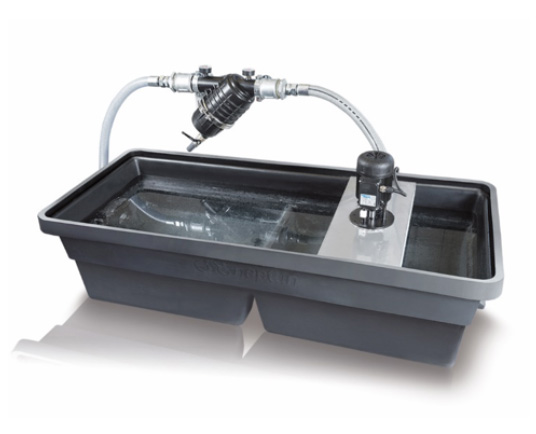
water tanks and filter for PVB
System with two 700-liter tanks to ensure good cooling with high-flow delivery pump and flow regulators for each spindle. Tubs in non-deformable and easy-to-clean polymeric material. Possibility of additional filter for intensive processing of laminated glass. Here they come
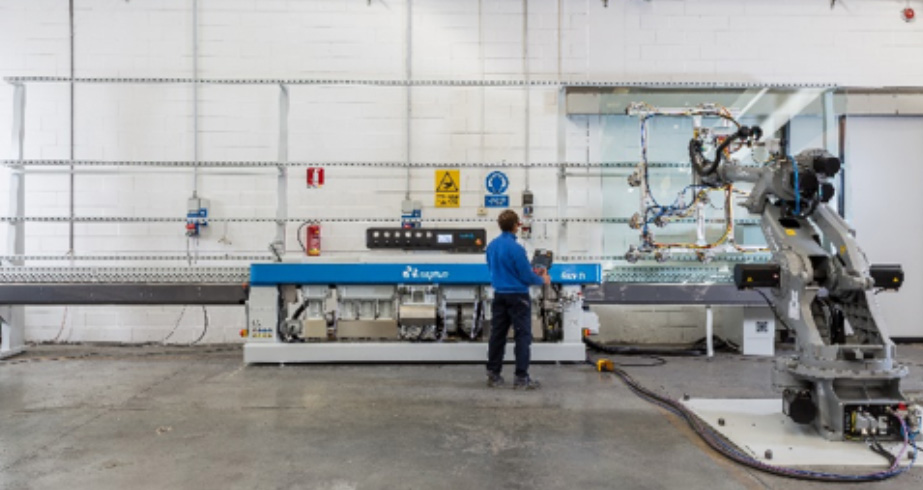
extended racks
Various dimensions of conveyors both in length and in height for processing large glass sheets
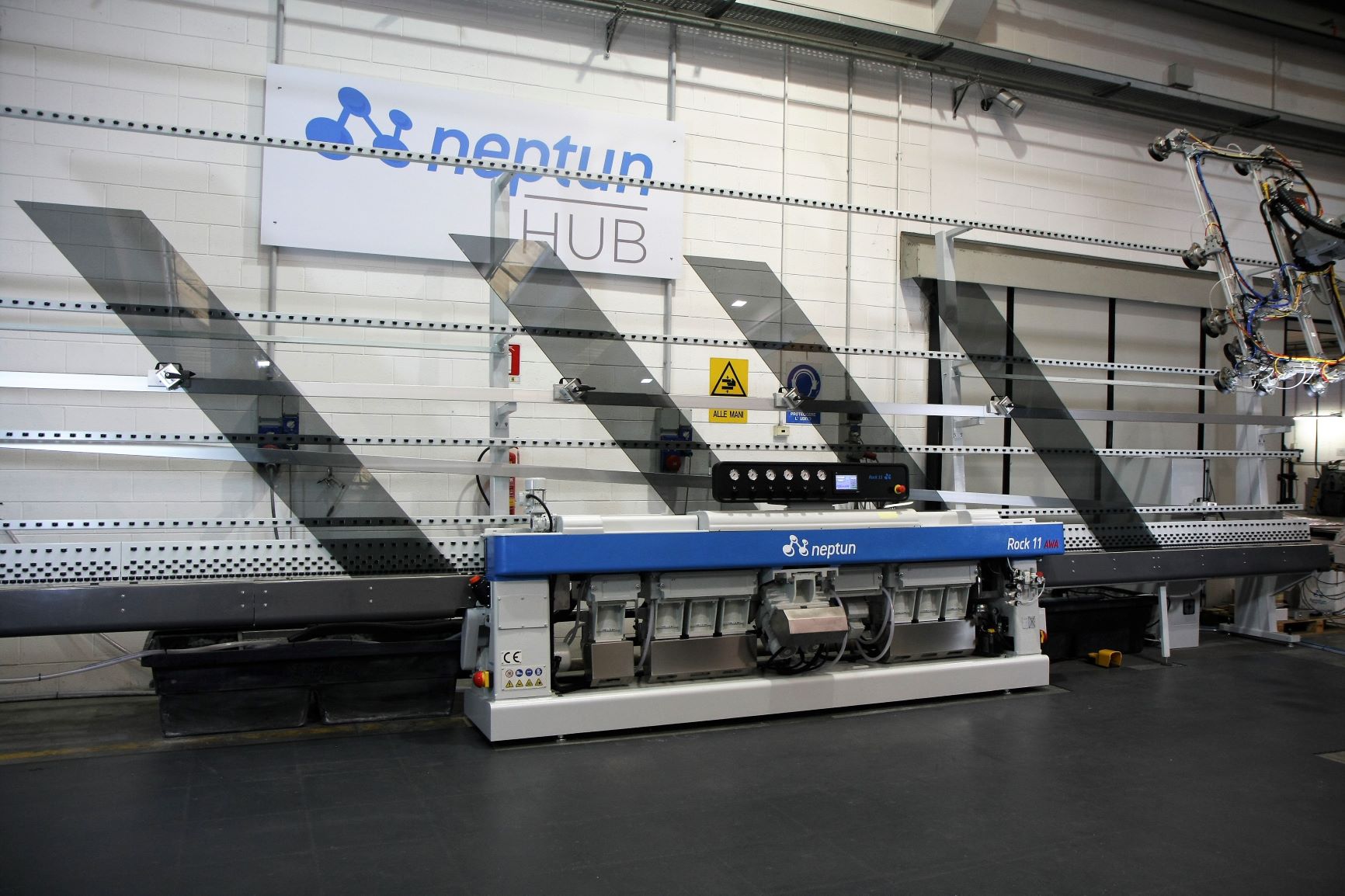
device for processing polygonal pieces
Practical device that allows the processing of polygonal geometries with angles up to 45 °. With this device the sheets are guided during all the loading, processing and unloading phases
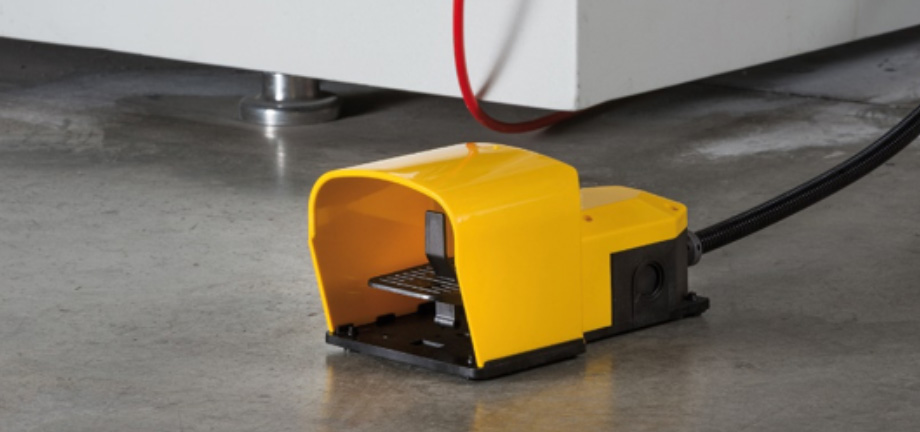
independent entrance conveyor motorization
An ergonomic pedal control allows you to stop and start the entrance to facilitate the loading phase of large or heavy slabs in total safety and without slowing down production
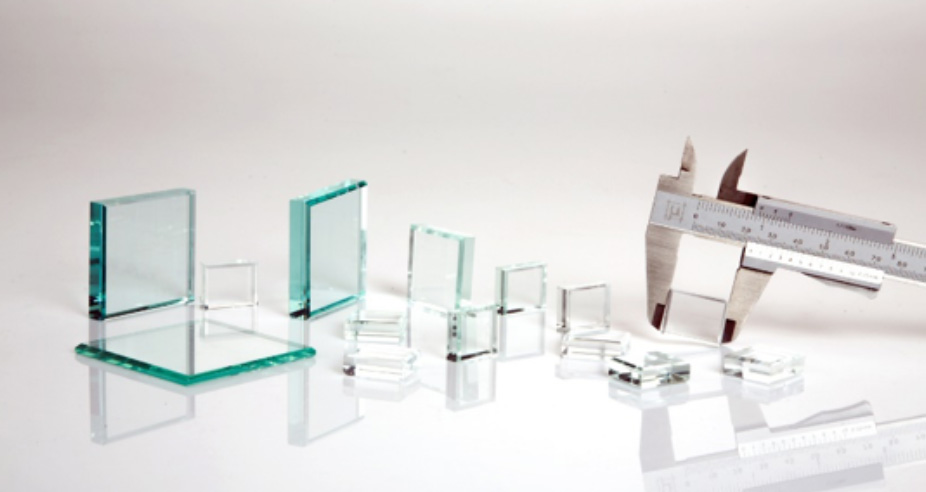
very small parts kit
Possibility of grinding very small pieces, up to 25mm in height, thanks to the optional loading device. The loaders can also be supplied for machines already installed
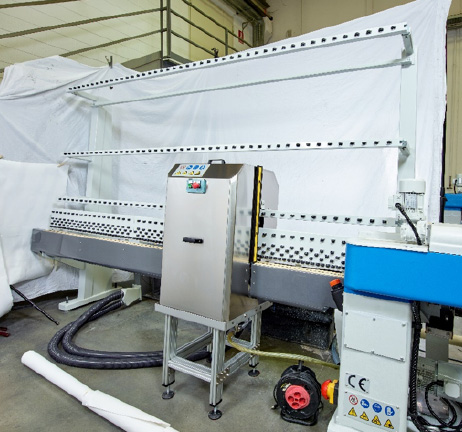
washing machine on outlet conveyor LV 322-40.
The washer dryer that can be mounted directly on the grinder outlet. Made entirely of stainless steel, it is fully automatic in its adjustment from 3 to 40mm thick